課程設計說明書
設計題目:熔模鑄造
系 部:機械工程系
目錄
摘要
1.零件的特點
1.1 零件圖
1.2 零件的結構工藝性分析
1.2.1 鑄件壁厚
1.2.2 鑄件結構
2.確定工藝參數和工藝方案
2.1 鑄件最小鑄出孔
2.2 鑄件尺寸公差
2.3 鑄件表面粗糙度
2.4 鑄件加工余量
2.5 基準面選擇
2.6 鑄件毛坯圖
3.壓型設計
3.1 裝配圖
3.2 壓型分類
3.3 分型面的選擇
3.4 型體設計
3.4.1 型體定位
3.4.3 型芯設計
3.4.4 壓型排氣
3.4.5 壓型加工精度
3.4.6 總裝技術要求
3.5 注蠟口
參考文獻
摘要本設計是通過熔模精密鑄造的方法來鑄造鑄件,先分析鑄件,進行工藝設計,確定了主要參數,進行壓型設計,繪制出鑄件工藝圖,進行熔模制造-型殼制造-脫蠟焙燒-熔煉澆注-后處理分析,結合具體零件,通過具體分析,最后有針對性的制定出材料為 ZL102熔模鑄造工藝方案。根據現實生產的應用,表明:熔模鑄造適用于實際生產中鑄件鑄造。 關鍵詞:鑄件;零件圖;熔模鑄造:工藝流
1.零件的特點1.1 零件圖圖1-1為零件圖,材料為鑄鋁,材料牌號:ZL102,不可熱處理強化,該合金的鑄造性能優良,無熱烈及疏松傾向,氣密性。 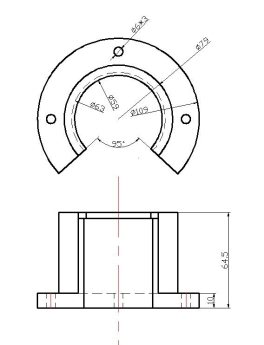
圖1-1 1.2 零件的結構工藝性分析熔模鑄件的結構工藝性是指,從熔模鑄造生產工藝角度出發,對零件結構提出的要求。也就是在滿足工作要求的前提下,希望零件結構能兼顧到熔模鑄造的工藝特點,使之盡量與熔模鑄造的工藝要求相吻合。 鑄件結構是否合理,對鑄件質量、生產工藝的可行性和簡易性以及生產成本等影響很大。熔模鑄件的結構應當符合熔模鑄造的生產特點。 1.2.1 鑄件壁厚由于熔模鑄造的型殼內表面層光潔,并且一般為熱型殼澆注,因此熔模鑄件壁厚允許設計得較薄。但鑄件壁厚應盡可能均勻,以減少熱節,便于補縮,為防止澆不足等缺陷,各種合金鑄件均規定有可鑄出的最小壁厚。表 1-1 為碳鋼的熔模鑄件的最小壁厚。 表 1-1 熔模鑄件的最小鑄出壁厚
本次設計為一鑄件,見圖 1-1,由上表得 ZL102熔模鑄造的最小壁厚為2.5mm。 1.2.2 鑄件結構由零件三維圖 1-2 可知,整個鑄件中,沒有工藝肋結構,有孔槽結構。熔模鑄件一端為平面,鑄件周邊有三個直徑為 6 的通孔,可以直接鑄造出來的。鑄件材料為 ZL102,收縮率為 0.8~1.0。該鑄件全部尺寸均為標注公差。按圖中要求,熔模鑄件鑄鋁的公差為 CT4~6 級。 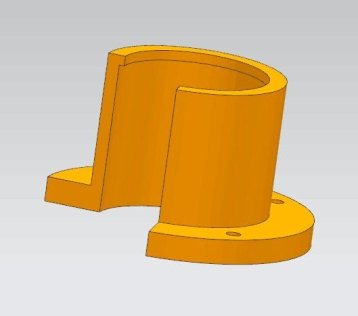
圖1-2三維圖 2.確定工藝參數和工藝方案2.1 鑄件最小鑄出孔熔模鑄件上三個小通孔,表 2-1 所示為正常鑄造情況下的最小鑄出孔的孔徑和深度。 表 2-1 熔模鑄造最小鑄出的孔徑與深度 本次設計的最小鑄出孔:直徑為Ø6mm,孔深為10mm 的通孔。 2.2 鑄件尺寸公差影響鑄件尺寸的因素很多,主要是熔模、型殼和鑄件三方面的尺寸變化(收縮和膨脹)這些變化中有些因素較為固定,有些則多變的,這就使得鑄件的尺寸在一定范圍內波動,波動范圍愈小,尺寸愈精確。成批和大量生產鑄件的尺寸公差按表 2-2 進行選擇。 表 2-2 成批和大量生產鑄件的尺寸公差 CT 由于此次設計的鑄造方法為熔模鑄造,合金的種類為鑄鋁,所以選用鑄件的公差等級為 CT4~6級。 鑄件尺寸公差是指允許的鑄件尺寸變動量。公差就是最大極限尺寸與最小極限尺寸代數和的絕對值。鑄件尺寸保持在兩個允許的極限尺寸之內,就可以滿足加工、裝配和使用的要求。根據鑄件的技術要求,鑄件尺寸公差應符合 GB/T 6414-1999 的 CT4-6級規定,查閱手冊得: 表 2-3 鑄件尺寸公差(mm) 根據毛坯的尺寸,鑄件尺寸公差值取 0.7mm。 2.3 鑄件表面粗糙度熔模鑄件表面粗糙度為RMS60~100,精整后可達 RMS40~100,但不同材質所獲得鑄件表面粗糙度不同,見表 2-4。 表 2-4 不同材質熔模鑄件表面粗糙度 RMS(單位10~6m) 本次工藝選用鑄鋁工藝,所以熔模鑄件的表面粗糙度為RMS60~100。 2.4 鑄件加工余量本鑄件的收縮率為 1.8~2.5%,所以鑄件整體基本無需加工,只用一個圓弧面需要加工,加工余量為 0.7mm 及三個圓孔需加工。 2.5 基準面選擇此鑄件為柱形通孔零件,需要三個端面才能約束 6 個自由度,選擇鑄件的下端面、左端面和后端面。 2.6 鑄件毛坯圖 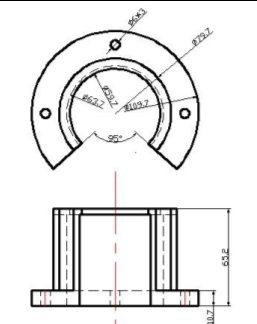
圖2-1毛坯圖 3.壓型設計3.1 裝配圖裝配圖如圖3-1所示: 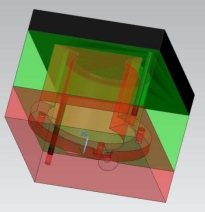
圖3-1裝配圖 上、中、下壓型三維示意圖,如圖 3-2、3-3 、3-4所示: 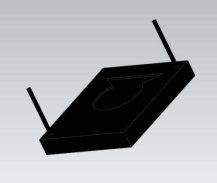
圖3-2上壓型三維結構示意圖 
圖3-3中壓型三維結構示意圖 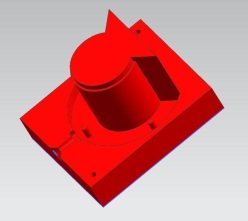
圖3-4下壓型三維結構示意圖 3.2 壓型分類(1)常用壓型的分類 1)機械加工壓型; 2)鑄造壓型; 3)塑料壓型和塑料鍍銅壓型; 4)石膏壓型; (2)由于機械加工壓型具有以下特點 1)材料:鋼、銅合金、鋁合金; 2)尺寸精度可以充分滿足設計要求,型腔表面粗糙度細; 3)使用壽命可達十萬次以上;由于本次設計的鑄造合金種類為銅合金,所以選用機械加工壓型。 (3)設計機械加工壓型應滿足的要求 1)裝拆方便,輕巧耐用,取模容易; 2)保證制出的易熔模能達到要求的尺寸精度和表面粗糙度; 3)壓型的各個零件均應符合機械加工要求,機械加工方便,經濟合理; 4)小件用一型多腔,以提高易熔模生產率; (4)機械加工壓型結構 機械加工壓型的機構主要由型體、型芯、抽芯機構、起模機構、定為導向機構、鎖緊機構以及排氣機構等組成。 由于本鑄件為一回轉體對稱結構,所以選有水平分型二開型。 3.3 分型面的選擇分型面是指壓型型體之間的界面,選擇不同的分型面會導致壓型結構不同,并直接影響到壓型加工的方便程度、使用性以及易熔模的生產率, 因此分型面選擇是壓型設計的關鍵問題之一。通過對閥體鑄件的分析, 我們可以輕易確定分型面, 設置這個分型面,觀察鑄件圖我們可以發現上中下型體的內腔是對稱的,在型體和型芯設計加工中就會大大地提高效率。 因此我們選擇如圖所示處為分型面。如圖 3-5所示。 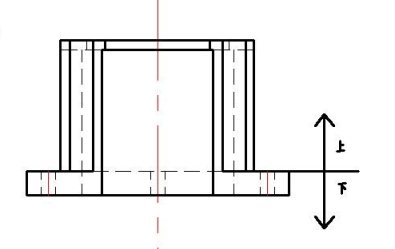
圖3-5分型面 3.4 型體設計3.4.1 型體定位上下型體之間的定位面一般需要設置兩個以上定位銷才能限制其自由度,但過多的定位銷會引起過定位。定位銷之間的間距越大,定位精度越高。在本設計中,采用 M8 的定位銷,如圖 3-6,其一在壓型左下方,另一個在其的右上方,才有布置距離兩側邊緣分別為 10mm 和10mm。具體的請見設計圖壓型裝備配。兩型體與圓柱銷的配合原則是,上型體與圓柱銷采用間隙配合,下型體與圓柱銷采用過盈配合。本設計中上型體與圓柱銷采用 H8/f7 的配合,下型體與圓柱銷采用 H8/s7 的配合,如圖3-6 所示。 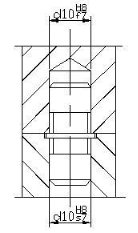
圖 3-6 型體定位 3.4.3 型芯設計構成熔模內部形狀的構件叫做型芯,型芯的成型部位的形狀隨易熔模熔模內腔形狀而定,但型芯的定位部位應盡可能的有規則。為了拔芯方便,型芯上均作出手柄部分。型芯可分為金屬型芯、尿素型芯、陶瓷型芯和石英玻璃型芯。本設計采用金屬型芯。如圖 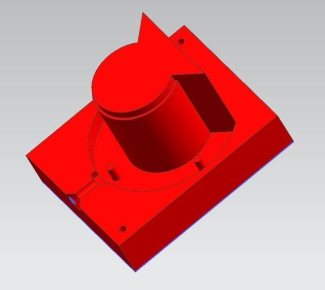
圖3-7型芯 3.4.4 壓型排氣模料注入壓型時如果型腔內的氣體來不及排除或者在型腔深處形成氣袋,往往會造成易熔模成形不良,因此壓型應該具有良好的排氣條件。設計中我們采用型芯間隙排氣,排氣部位在型芯與型體的相配處。 3.4.5 壓型加工精度3.4.6 總裝技術要求1.分型面間隙不大于 0.05mm; 2.各組合塊及上下型錯位不大于 0.05mm; 3.頂桿不高于型腔表面,可低于型腔表面 0.05mm 以內;復位桿不高于分型面,可低于分型面 0.05mm 以內; 4.型腔表面無凸凹不平及毛刺等缺陷,型腔邊緣應保持銳角; 5.總裝后經壓蠟試模,取模時應無卡阻現象,蠟模飛邊厚度不大于 0.05mm; 6.壓型外表邊緣應成銳角,并打上零件號,制造日期和其它標志。 3.5 注蠟口注蠟口是壓制蠟模時蠟料的通道。注蠟口選擇時要考慮以下因素: 1.最好設置在鑄件內澆口上,或設置在鑄件的加工面上; 2.注蠟口的位置要保證輸入蠟液流暢,型腔各處流程不長,并且最好設置在最大壁厚處。 3.注蠟口的設置,要盡量使壓 型結構簡單,操作方便,取模可靠、順利; 4.薄壁處盡量不設注蠟口,以免拉裂。 注蠟口的形式隨注蠟器的形狀而定,注蠟口直徑一般為 3~10mm,本壓型注蠟口直徑 6mm,外圓直徑 12mm。角度為 60°。
完整的Word格式文檔51黑下載地址:
材料1502班熔模鑄造課程設計.docx
(208.92 KB, 下載次數: 5)
2018-7-10 09:37 上傳
點擊文件名下載附件
下載積分: 黑幣 -5
|