目錄目錄
1 緒論
1.1汽車涂裝在生產的重要應用
1.2汽車涂裝線的發展
1.3目前涂裝線存在的問題
1.4研究的目的和意義
1.5本文的主要研究內容和工作
2 汽車涂裝線的組成
2.1 電泳技術
2.2 汽車涂裝技術要求
2.3 涂裝線基本組成部分的作用
2.4對涂裝線自動控制系統的要求
3 涂裝線自動化行車
3.1自動化行車基本運行情況
3.2自動化行車的設計要求
3.3繼電接觸控制自動化行車
4 PLC控制自動化行車
4.1可編程控制器技術
4.1.1可編程序控制器的工作原理和分類
4.1.2可編程序控制器的特點
4.2 PLC控制自動化行車
4.3 PLC控制設計
4.3.1生產工藝流程
4.3.2 電氣原理圖
4.3.3程序編寫
5 結束
5.1 結論與展望
5.2 PLC的工業自動化
1 緒論
1.1汽車涂裝在生產的重要應用涂裝對于汽車制造來說有兩個重要作用:1、增強汽車的防腐蝕能力。2、增加汽車的外觀美。據資料表明,國內外每年因金屬銹蝕造成的損失相當驚人。由世界銀行提供資料表明,1996年美國國民總產值為74335億美元,因金屬腐蝕損失約為2000億美元,約占國民生產總值的2.7%。而汽車是以鋼材金屬為主的工業制品,若不能很好解決金屬腐蝕問題,將嚴重影響汽車的使用壽命和外觀,因此汽車自問世,就與涂裝結下了不解之緣。
1.2汽車涂裝線的發展國內汽車涂裝業主要經歷了以下幾個階段:
1、五十年代到六十年代中期,國內只有長春第一汽車廠一個專業制造汽車的廠家,汽車涂裝主要是引進前蘇聯的汽車車身涂裝生產線,操作方式均為手工操作,噴漆室為簡易的側抽風水幕式,輸送方式采用普通懸掛鏈,涂裝工藝水平不高。
2、六十年代中期到八十年代中期,隨著國外汽車的發展以及國內二汽和上汽的建成投產,汽車涂裝技術有了一個大的提高,開發并采用了陽極電泳涂裝以及濕碰濕面漆涂裝工藝,表面活性劑清洗、輻射烘干和靜電噴涂等涂裝技術。
3、八十年代中期到九十年代中期,隨著轎車生產線的引進,國內汽車涂裝技術也進入了前處理磷化處理、陰極電泳涂裝和面漆自行靜電噴涂等先進涂裝技術。
4、九十年代中期到現在,隨著歐美日不同系統的轎車車型的不斷引進,我國轎車進入規模化、現代化的生產階段,汽車涂裝技術水平也跨入了世界較先進行列,機器人自動靜電噴涂技術、全浸式磷化處理、陰極電泳涂裝技術、滑撬輸送系統、集中送排風的大型上送風下抽風噴漆室、帶廢氣處理的燃燒爐(TAR)烘干爐系統、中央控制技術等國際先進的汽車涂裝技術和裝備在轎車涂裝行業得到了廣泛的應用和發展。由于國內重型載貨汽車行業都是國內廠家自主研制的產品,生產設備要求不高,自動化程度不高,沒有采用機器人自動靜電噴涂,沒有在前處理電泳底漆線采用雙工位生產方式,多品種柔性化生產情況,重型載貨汽車涂裝線技術還處在一個比較低的技術水平。
1.3目前涂裝線存在的問題目前涂裝線系統主要采用由繼電器接點控制系統,其缺點:由于采用固定接線形式沒有靈活性和通用性,在工藝要求提出后才能實現系統化生產,并且采用觸點開關動作,動作有延時并伴有電弧產生,造成觸點損壞,以致動作不可靠維護不方便。而且浪費了大量的勞動力資源,不利于工業自動化的發展。
1.4研究的目的和意義工業自動化是現在和未來工業發展的必然之路。對于涂裝線生產,涂裝設備的發展很快,不斷有新技術現,不可能大量更新裝備,舊的裝備還需要在一段時間內發揮其潛力,這就需要在舊裝備上進行一定的改造。在電泳涂裝生產線中引入PLC工業控制技術,使原有設備可靠性、穩定性得到改善,降低了工人的勞動強度,提高了生產效率,為今后電泳涂裝生產線的改造提供了參考。
1.5本文的主要研究內容和工作本文主要通過對目前汽車行業涂裝線存在的一些不方便進行改進設計,引入現在常用的PLC來控制涂裝過程,比起以前的人工控制節省了時間提高了工作效率,產品產量得到極大提高,而且利用自動控制設備完成的噴涂工作噴涂質量好,延長了使用壽命。
第一章主要介紹了汽車涂裝在汽車生產中的重要性,以及目前汽車行業涂裝線的組成及其存在的一些缺點。
第二章系統介紹汽車涂裝線的組成,包括技術要求、參數設定和一些基本概念,是引進PLC控制的前提。
第三章著重闡述涂裝線中自動化行車的運行原理和工作職能,并且在目前涂裝線中引入自動化行車的現實意義,是本文的重要部分。
第四章重點介紹使用PLC控制自動化行車,其中有PLC的設計編程、控制布線、工藝設計等,是整篇文章的重中之重。
第五章主要對PLC在以后的自動化控制中做一個瞻望,以及對本設計的一個總結。
2 汽車涂裝線的組成汽車涂裝車間的控制系統主要分為三個層次:監控層,控制層和設備層。每個層次使用不同的網絡結構及相應的軟硬件配置,以實現不同的功能。(本文只討論控制層的設計,不涉及其他層的開發研究。)控制層主要采用PLC控制單元以及現場總線接受來的現場數據(數字信號或模擬信號),經過PLC內的存儲的控制程序的運算和處理后,發出相應的指令(輸出信號)對現場設備進行控制。
涂裝線主要由以下部分組成。
(1)前處理—電泳線:包括前處理、電泳、電泳后沖洗、電泳烘干室及強冷室等。
(2)PVC線:包括粗細密封照明工位、PVC噴膠室、PVC烘干室及強冷室等。
(3) 中涂線:包括底漆打磨室、中涂擦凈噴漆室、晾干間、中涂烘干室等。
(4)面漆線:包括鈑金修理、中涂打磨間、面漆擦凈噴漆室、晾干間、面漆干室及強冷等。
(5)修飾噴蠟點修補線:包括面漆修飾工位、噴蠟間、點修補。
涂裝流程如圖2.1所示。
圖 2.1 涂裝流程
2.1 電泳技術電泳就是溶液中帶電粒子(離子)在電場中移動的現象。利用帶電粒子在電場中移動速度不同而達到分離的技術稱為電泳技術。1937 年瑞典學者 A.W.K.蒂塞利烏斯設計制造了移動界面電泳儀 ,分離了馬血清白蛋白的3種球蛋白,創建了電泳技術。在確定的條件下,帶電粒子在單位電場強度作用下,單位時間內移動的距離(即遷移率)為常數,是該帶電粒子的物化特征性常數。不同帶電粒子因所帶電荷不同,或雖所帶電荷相同但荷質比不同,在同一電場中電泳,經一定時間后,由于移動距離不同而相互分離。分開的距離與外加電場的電壓與電泳時間成正比。
按分離原理的不同,電泳分為 4類:移動界面電泳、區帶電泳、等電聚焦電泳和等速電泳。
本文所研究的涂裝生產就是利用電泳技術完成對工件的涂裝。
2.2 汽車涂裝技術要求生產方式:空中積放鏈
工件類型:車身
電泳方式:陰極電泳
工序:如表2.1所示。
表 2.1 生產工序
2.3 涂裝線基本組成部分的作用(1)前處理:車件用鑄鋼制造而成,由于在制造過程中的現場工藝,以及鋼鐵本身的特點極易造成車件生銹沾染油污,電泳前必須做除銹、除油、除酸、脫脂等處理。
(2)電泳:將前處理后的車件放入電泳液中電泳,使車件完成涂漆工作。
(3)烘干:將電泳完的車件送入烘干爐做烘干處理。
(4)滑橇:傳動設備,作用于前處理、電泳和烘干的整個過程,與各個過程配合完成整個車件涂裝工作。
2.4對涂裝線自動控制系統的要求(1)電泳槽液的溫度控制。按照設定值進行溫度自動控制,保證槽液溫度范圍在29~31℃之間。
(2)出槽噴淋。在純水洗、電泳、UF1 水洗、UF2 水洗工位,當工件出槽時,根據工藝要求自動識別工位,進行相應的新鮮純水或超濾水槽上噴淋,提高和改善涂膜表面質量,減輕二次流痕。
(3)電泳。按照定長時間分兩段通不同的電壓值,使槽液中的成膜物質泳涂到工件表面上。
(4)極液電導率控制。按照設定值850μs/cm自動控制。
(5)槽液液位控制。通過液位計、電磁閥實現PLC 對電泳槽、極液槽的液位控制。
(6)各電動機的手動、自動起動和停機。
(7)實施監測并顯示各設備的運行情況,可實現對生產線幾個故障信息的自動聲光報警。
3 涂裝線自動化行車自動化行車具有自動化程度高、承載大、運行可靠、輸送工件體積大、工件垂直升降、節省空間、適用多種工況等諸多優點,在許多自動化生產線得到推廣和應用,如大型客車的車身、汽車的車架前處理自動化生產線,大規格型材表面處理自動化生產線、大型工件表面處理自動化生產線等,完全實現生產自動化,徹底解決了在這些惡劣生產線環境下工作時,存在的生產效率低、勞動強度高、對操作人員產生身體傷害等問題。自動化程控行車由機械作業系統和自動化控制兩部分組成。其中機械作業系統包含有垂直升降機構、運行機構、安全裝置、結構件等部分;自動化控制部分包含有上位監控機、PLC、變頻器、檢測元件等硬件部分以及管理程序、控制程序、故障檢測程序等軟件部分。
3.1自動化行車基本運行情況電鍍車間自動化行車是涂裝車間專門為提高生產效率、促進生產自動化和減少勞動強度,提出制造的一種專用自動起吊設備。它采用遠距離控制,起吊重量可根據實際情況選擇合適的電動機。起吊物品是待進行電鍍及表面處理的各種工件。其具體流程圖如圖3.1所示。
圖3.1 自動化行車流程示意圖
電鍍車間有多個電鍍槽,其作用各部相同,本系統只考慮五個電泳槽作用,分別為脫脂、酸洗、電泳、水洗。實際情況是根據生產方需要具體設定。本文設計五個電泳槽,分別標記為1槽、2槽…5槽。
在電鍍生產線一側,工人將待電鍍零件裝入吊籃,并發出信號,自動化行車便提升,到一定高度后自動逐段前進。按工藝要求在需要停留的的槽位停止,然后自動下降,停留一段時間后再自動提升,再前進。如此反復,完成電鍍工藝規定的每一個工序,直到生產線末端,自動返回原位。
設備的機械結構與普通小型車身結構相似,跨度較小,但要求準確停穩,以便吊籃能準確進入電鍍槽。工作時,自動化行車除了能前進/后退與吊籃提升/下降運動外,還能調整吊籃小車的左右移動。
3.2自動化行車的設計要求本系統由三臺電動機控制完成,而且每臺電動機都能實現正反轉功能,分別由KM1、KM2控制電動機M1的正反轉,由KM3、KM4和KM5、KM6分別控制前進后退電動機M2和升降電動機M3的正反轉。
左右行電動機M1為短時點動工作,故不需要設過載保護,而M2、M3則有相應的熱繼電器保護
主電路有隔離開關QF控制。
為保證準確停位,M2與M3不會同時工作,有互鎖作用,并且可以用同一直流電源實現能耗制動。
考慮到升降運動有一定的重量,在行車平移中需設置電磁閥抱閘制動。
3.3繼電接觸控制自動化行車繼電接觸控制可以較好地完成設計工藝要求,而且成本比較低、易操作,在一些要求不高的生產線中得到了廣泛的應用。常用的繼電接觸電器主要有接觸器、繼電器、熔斷器、斷路器和隔離器等等。由于繼電器順序邏輯控制系統有大量的活動觸點和元器件,只要其中任一部件或觸點故障,將造成系統的故障。另外,它的體積和重量較大,維修的工作量也較大。因此在某些自動化程度較高的生產系統中繼電接觸控制就不再滿足要求,PLC控制就隨之而產生。
4 PLC控制自動化行車
4.1可編程控制器技術可編程序控制器(PLC,Programmable Logic Controller)是由早期繼電器控制系統與微型計算機技術相結合而產生的,它是以微處理器為主的一種工業控制儀表,它融計算機技術、控制技術和通信技術于一體,集順序控制、過程控制和數據處理于一身,可靠性高、功能強大、控制靈活、操作維護簡單。為了使其生產和發展標準化,美國國際電工委員會于1952年頒布了可編程序控制器標準草案,1985年提交了第二版,1987年的第三版對可編程序控制器作了如下的定義:“可編程序控制器是一種專門為在工業環境下應用而設計的數字運算操作的電子裝置。它采用可以編制程序的存儲器,用來在其內部存儲執行邏輯運算、順序運算、計時、計數和算術運算等操作的指令,并能通過數字式或模擬式的輸入和輸出,控制各種類型的機械或生產過程。可編程序控制器及其有關的外圍設備都應該按照易于與控制系統形成一個整體,易于擴展其功能的原則而設計。”總之,可編程控制器也是一臺計算機,它是專為工業環境應用而設計制造的計算機。它具有豐富的輸入/輸出接口,并且具有較強的驅動能力。但可編程控制器產品并不針對某一具體工業應用,在實際應用時,其硬件需根據實際需要進行選用配置,其軟件需根據控制要求進行設計編制。隨著微電子技術、大規模集成電路技術、計算機技術和通信技術等的發展,PLC在技術和功能上發生了飛躍。在初期邏輯運算的基礎上,增加了模擬量和PID調節等功能模塊,形成了數值運算、閉環調節。尤其是PLC把專用的數據高速公路(HIGHWAY)改成通用的網絡,并逐步對各PLC生產廠家之間的通信規約規范化,使得PLC有條件和其它各種計算機系統和設備實現集成,以組成大型的控制系統,也使PLC系統具備了DCS的形態,使得PLC的應用拓展到連續過程控制領域,基于PLC的DCS系統目前在國內外都得到了廣泛的應用。
4.1.1可編程序控制器的工作原理和分類當PLC投入運行后,其工作過程一般分為三個階段,即輸入采樣、用戶程序執行和輸出刷新三個階段。
(1)輸入采樣——檢查各輸入的開關狀態,將這些狀態數據存儲起來為下一階段使用。
(2)執行程序——然后PLC按用戶程序中的指令逐條執行,但是把執行結果暫時存儲起來。
(3)刷新輸出——按第一階段的輸入狀態,在第二階段執行程序,在本階段將確定的結果輸出予以刷新。
完成上述三個階段稱作一個掃描周期。在整個運行期間,PLC的CPU以一定的掃描速度重復執行上述三個階段。PLC對信號的輸入、數據的處理和控制信號的輸出分別在一個掃描周期的不同時間進行的方式有助于排除系統受到的干擾。
可編程控制器的設計思想是盡可能地利用當前先進的計算機技術去滿足用戶的需要,PLC與繼電器接觸器控制電路的一個本質區別就是除了必要的與外部物理世界的接口(即I/0點)外,其它的邏輯功能均在其內部實現。這些邏輯功能不僅可以取代,而且遠遠超過諸如中間繼電器、時間繼電器等硬件邏輯所能達到的功能,從而為PLC在可靠性和便利性上形成特色奠定了基礎。
根據PLC的功能可分類如下:
(l)邏輯控制。
(2)定時控制。
(3)計數控制。
(4)步進(順序)控制。
(5)PID控制。
(6)數據控制:PLC具有數據處理能力。
(7)通信和聯網。
(8)其它:PLC還有許多特殊功能模塊,適用于各種特殊控制的要求,如:定位控制模塊,CRT模塊。
4.1.2可編程序控制器的特點PLC的主要特點可概括如下:
1、高可靠性
(1)所有的I/O接口電路均采用光電隔離,使工業現場的外電路與PLC內部電路之間電氣上隔離。
(2)各輸入端均采用濾波器,其濾波時間常數一般為10~20ms。
(3)各模塊均采用屏蔽措施,以防止輻射干擾。
(4)采用性能優良的開關電源。
(5)對采用的器件進行嚴格的篩選。
(6)良好的自診斷功能,一旦電源或其他軟、硬件生異常情況,CPU立即采取有效措施,以防止故障造成的損失擴大。
(7)大型PLC還可以采用由雙CPU構成冗余系統或者三個CPU構成表決系統,使可靠性更進一步提高。
2、采用模塊化結構
為了適應各種工業控制需要,除了單元式的小型PLC以外,絕大多數PLC均采用模塊化結構。PLC的各個部件,包括CPU、電源、I/O等均采用模塊化設計,由機架及電纜將各模塊連接起來,系統的規模和功能可根據用戶的需要自行組合。
3、豐富的I/O接口模塊
PLC針對不同的工業現場信號,如開關量或模擬量、交流或直流、電壓或電流、脈沖或電位、強電或弱電等,都有相應的I/O模塊與工業現場的器件或設備等直接連接,如按鈕、行程開關、接近開關、傳感器及變送器、電磁線圈、控制閥等。另外,為了提高操作性能,它還有多種人—機對話的接口模塊;為了組成工業局部網絡,它還有多種通訊聯網的接口模塊,等等。
4、編程簡單易學
PLC的編程大多采用類似于繼電器控制線路的梯形圖形式,對使用者來說,不需要具備計算機的專門知識,因此很容易被一般工程技術人員所理解和掌握。
5、安裝簡單,維修方便
PLC不需要專門的機房,可以在各種工業環境下直接運行。使用時只需將現場的各種設備與PLC相應的I/O端相連接即可。各種模塊上均有運行和故障指示裝置,便于用戶了解運行情況和查找故障。由于采用了模塊化結構,一旦系統中某模塊發生故障,用戶可以通過更換模塊的方法,使系統迅速恢復運行。
4.2 PLC控制自動化行車PLC要完成自動化行車控制系統的功能
(1)開關量輸入:如電動機手動/自動控制信號、電動機過載信號、工件到位信號、外圍設備運行/故障信號、電磁閥手動信號、液位信號等通過24V 電壓與PLC 輸入端相聯。
(2)模擬量輸入:分別通過熱電阻、電導率變送器對槽液溫度、極液電導率等信號進行采樣,經智能數字調節儀的輸出繼電器輸出開關量信號,送入PLC輸入端構成閉環控制回路,使溫度和電導率自動地穩定在符合工藝要求的設定值上。
(3)開關量輸出:控制設備的起動或停止、開或關,如噴淋電磁閥、冷卻電磁閥、液位控制電磁閥、分段整流信號、循環泵、送排風機起停、外圍設備運行/故障指示及聲光報警等。
(4)自動化任務:能夠根據工藝要求完成各種操作。自動化程序能快捷無誤地進行,而且在系統出現錯誤時能有自動報警、糾錯和記憶功能,能完成對錯誤的改正、阻止。每次任務能有自動和手動兩種方式。
4.3 PLC控制設計4.3.1生產工藝流程本系統有5個槽,在槽1處為裝料位,工人將車架裝入吊籃,并發出信號,自動化行車便提升并逐段前進。按工藝要求在每個槽停止,并自動下降,停留一段時間后自動上升,如此完成每道工序。最后繼續前進到槽5,結束任務,并發出信號,自動返回。如圖4.1所示。
圖4.1 工藝流程圖
4.3.2 電氣原理圖(1)主電路圖
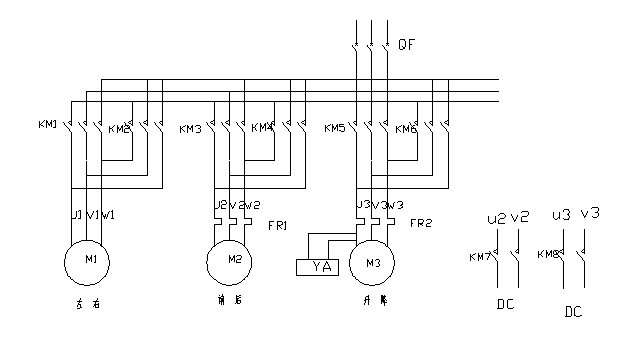
圖4.2 電氣主接線圖
(2)電氣安裝板元件布置示意圖
圖4.3 安裝布置圖
(3)控制電路表
表4.1 PLC輸入/輸出地址分配表
4.3.3程序編寫本文只對其中幾個重要的典型的程序編寫討論
(1)自動手動控制
Network 1
LD I1.0
A I0.0
A I0.6
O M0.0
A I1.1
= M0.0
Network 2
LD M0.0
CALL SBR0
(2)左右行電機能耗制動
Network 1 //
LDN Q0.5
ON Q0.6
TOF T47, 100
Network 2
LDN Q0.5
AN Q0.6
A T47
= Q0.7
(3)槽3的運行控制
Network 1
LD I0.2
= M1.0
Network 2
LD M1.0
AN Q0.5
AN Q0.6
AN Q1.1
= Q1.2
Network 3
LD I0.6
= M1.1
Network 4
LDN M1.1
TOF T37, 1200
= Q0.5
= Q0.6
Network 5
LDN Q0.5
AN Q0.6
AN Q1.2
A T37
5 結束5.1 結論與展望工業自動化是現在和未來工業發展的必然之路。對于涂裝線生產,涂裝設備的發展很快,不斷有新技術出現,不可能大量更新裝備,舊的裝備還需要在一段時間內發揮其潛力,這就需要在舊裝備上進行一定的改造。在電泳涂裝生產線中引入PLC工業控制技術,使原有設備可靠性、穩定性得到改善,降低了工人的勞動強度,提高了生產效率,為今后電泳涂裝生產線的改造提供了參考。
用PLC對電鍍生產線進行自動控制,簡化了電氣控制系統的硬件和接線,提高了控制系統的靈活性、可靠性,增強了系統的抗干擾能力,使系統功能完善、操作簡單、安全穩定、維護量小. 經模擬調試,手動、單步、單周期、連續四種工作方式均可正常可靠運行.
傳統PLC用戶程序都是放在一個統一的程序單元中,現在可以進行多模塊組織,把程序分解成不同的、功能較單一的小程序、函數或功能塊,以塊為單位設計及調試,然后再按照需要用主程序去調用這些塊,以期達到以下目標:
(1)程序邏輯清晰,可讀性強;
(2)程序便于更改,可改性好;
(3)程序標準化,可移植性強;
(4)實現多人參與編程,提高編程的速度。
5.2 PLC的工業自動化整個涂裝車間的輸入/輸出信息形式多樣(包括圖像、圖形、文字、語音、數字等多媒體形式),信息量大,對系統功能要求高。控制監視任務不僅僅限于單機的檢測和控制問題,而且還實現了對整個車間的監控、故障診斷、物流優化、生產預報和調度。以PLC和計算機為核心的信息處理機制完成對綜合信息的管理、生產過程的計劃、調度、監視與自動化控制。這就是所謂的“全集成自動化”,“全集成自動化”就是在生產自動化過程中,提高效率,降低成本的全面解決方案。在“全集成自動化”中,PLC結合PC解決方案,自動化計算機,人機界面系統,運動控制,以及分布式系統等。其數據管理,通信,組態和編程三者有一致的數據庫和通信協議等,形成一個整體。這種三重一致的集成擴展到整個自動化領域。目前,國內外的汽車制造業乃至整個制造業自動化控制技術都向著這種“全集成自動化”發展。
目前,我國汽車工業涂裝生產技術的發展較國外先進技術在不斷縮小,但仍有很大的差距,使用總線控制技術,以太網控制技術在國內汽車廠使用的仍然不夠充分,所以我們瞄準國內外技術前沿,搶占技術制高點,開發采用了各種先進的控制技術的涂裝生產線,其穩定和高效的運行必將帶來重要商機,對于促進汽車行業的發展、引導汽車工業生產線高端自動化控制的發展都具有深遠的意義。
完整的Word格式文檔51黑下載地址: